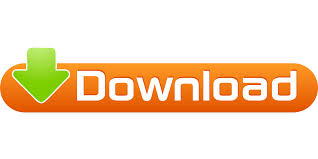
- Cutviewer mill cutter radius compenstaion how to#
- Cutviewer mill cutter radius compenstaion manuals#
- Cutviewer mill cutter radius compenstaion install#
- Cutviewer mill cutter radius compenstaion full#
Cutviewer mill cutter radius compenstaion full#
No clue about newer controls but T+ and older controls, but anytime you are profiling with a groove tool (groove insert with flat), the machine does not recognize it as a grooving tool, but rather a full radius tool and comps the cutter accordingly. And so creates a toolpath base on the front corner radius only.Not exactly. The new problem now is I have and MDT tool but if I use it to profile with it ignores the width of the insert. I'm not there yet but It is getting easier. (better with linear motion), try to draw the contour with or without cutter compensation or with differ radius.Well that's what I've heard.
Cutviewer mill cutter radius compenstaion install#
Try to install a marker pen in one of you tool holder, manully load it into spindle, clamp/fix a wood board on the m/c table with a white paper.call a simple program with G41/G42.G40. and length compensation will be actived when Z axis begins to move(G1/G0.Z.) It no need be D number as same as T number, however people like do that as it is easy to remeber.ģ) suggestion to try effect of cutter radius compensation on your m/c: Normally mill cutter only use 1 D per Tool, the radius input will be active as metioned in Q 1). programmed or generated in the same line=SAME BLOCK with G41/g42/g40, the cutter radius compensation will be activated until there is motion block=G1/G0. I guess I'll start with these two questions and maybe follow up with more if I get some responsesĪny help would be greatly appreciated, thank you,ġ) It doesn't matter G0,G1. Question: What doesthe cutting edge number (D)represent? 50" End mill / where a nominal gage length and radius are input) and a value input into the tool offset data set (I'm not sure what this value is - is it the difference between nominal and actual, or is it the actual value of the radius). I'm guessing that the difference between the nominal toolradius and the actual toolradius is represented in the difference between the parameters used to define a particular tool - by its group and type (ex. It does appear as though the posted code tells the controller what the nominal value ofa particular tool is.
Cutviewer mill cutter radius compenstaion manuals#
Question:Is this approach for calling the cutter comp command correct? One thing that concerns me is that the post does not add a G0, G1, G17code in the same line where G41 is output - the examples I've seen the Siemens manuals have this code in the same line asthe G4x code.Īfter reading through the manuals I am still unclear as to how the calculation is is made to offset the tool path when cutter comp is activated. Looking through the code after it is post-processed I can see the following: The PPWordI input, was CUTCOM/LEFT, # (where #is the D register number, 5 in my case,correspondingtothe offset D registerfor tool 5 -T5).The PPWordisinvokedafter an axial move to a plane where the elongated profile countour will be cut with a linear move directly after.CUTCOM/OFFthe same way. Using CATIA, inmy approachmacro, I've added the PPWord(s) to turn on cutter comp left. I've createda simple program to cut an elongated hole. Listed below are a few questions I could use some help with. I've looked through aboutfive of the Siemens programming manuals but I'm still unclear as to what the controller is doing in the background.
Cutviewer mill cutter radius compenstaion how to#
Hello, I am pretty new to the 840D controller and I'm trying to figure out how to get cutter compensation working.
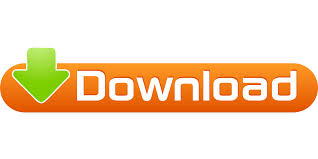